PRODUCȚIA DE BATERII: cum este fabricată inima unei mașini electrice ŠKODA?
Cum sunt fabricate bateriile pentru hibrizii plug-in ŠKODA? De ce angajații au nevoie de haine speciale de lucru? Pentru ce au nevoie de un marker obișnuit? Și de ce cântăresc șuruburile?
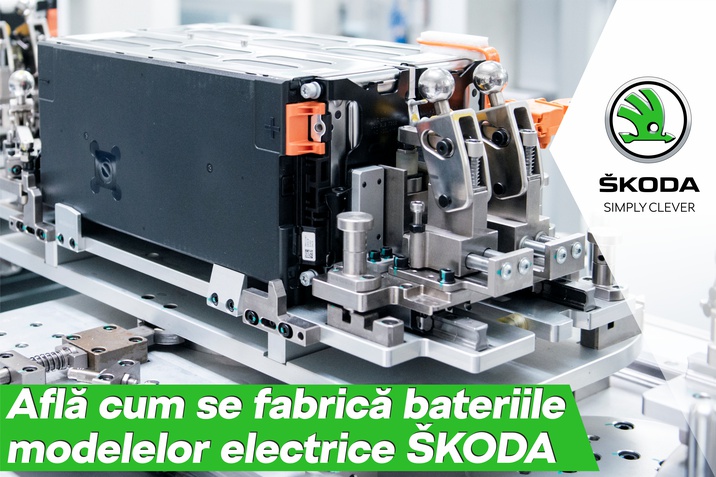
Linia de producție furnizează baterii litiu-ion pentru modelele hibride plug-in ŠKODA SUPERB iV și ŠKODA OCTAVIA iV. De acolo, bateriile își fac drum și în mașini făcute de alte companii ale grupului Volkswagen. Capacitatea liniei de producție de ultimă generație și puternic automatizată este de 180.000 de baterii pe an.
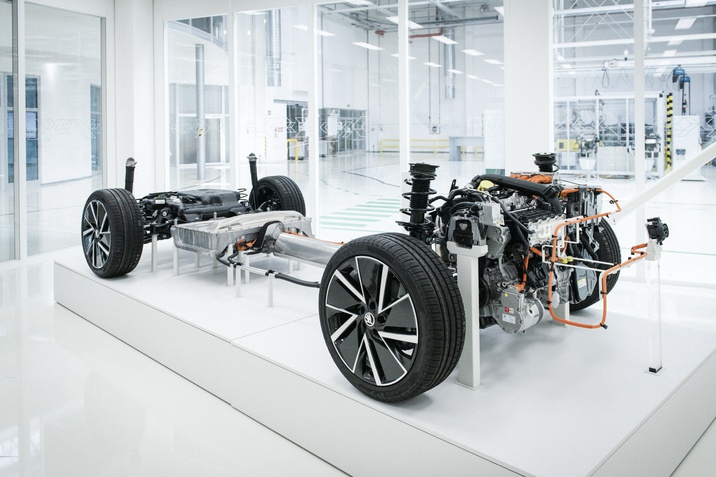
TREI DIRECȚII
În fabrica foarte bine luminată, aerisită și spațioasă, linia de producție a bateriilor arată ca o linie unică, simplă la prima vedere. Însă ea are trei secții principale, bateriile finite fiind scoase aproximativ la mijloc. Modulele bateriei sunt reunite în ansamblul de patru într-una din secții. Într-o altă secție este realizată carcasa complet echipată, care adăpostește modulele bateriei și este perfect sigilată la sfârșitul procesului de asamblare pentru a proteja bateria de influențele externe. Electronica bateriei este alcătuită în a treia secție, de dimensiuni mai mici.
La asamblarea celor patru module ale bateriei, ŠKODA utilizează module de la un furnizor extern care sunt de fapt celule mici de baterii. Aceste module continuă de-a lungul primei părți a liniei în două fluxuri paralele: pentru partea stângă și dreapta a bateriei separat. Fiecare modul provine de la furnizor încărcat cu o capacitate de aproximativ 20%, astfel încât măsurile de siguranță sunt necesare chiar de la începutul procesului de producție. Primul pas este învelirea modulului cu folie termoreductoare specială care ajută la îmbunătățirea răcirii întregului set de baterii. Între module este introdus un sistem de răcire - odată conectat, lichidul de răcire circulă prin acest sistem.
Alte părți ale liniei gestionează electronica de joasă tensiune ale bateriei. Întregul modul de control, cunoscut sub numele de e-box, cu unitatea de control proprie, este realizat într-o zonă a liniei de producție cu o protecție sporită împotriva oricărui exces de tensiune electrostatică. De aceea, toți cei implicați în acest proces poartă haine speciale.
„Pardoselile, îmbrăcămintea și încălțămintea care trebuie să fie certificate ESD și trebuie testate în mod regulat pentru a verifica dacă acestea sun protejate împotriva electricității statice sunt esențiale pe întreaga linie de producție”, explică Otakar Mašek, specialist în asambalrea bateriilor. Componentele individuale de pe linie sunt, de asemenea, special protejate.
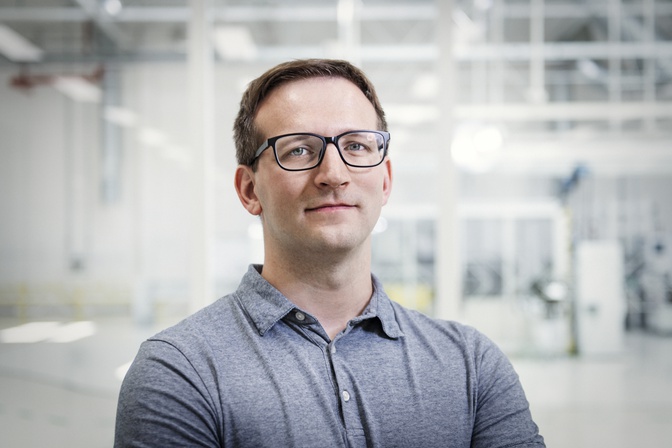
O SINGURĂ PIESĂ DIN ALUMINIU
În timp ce modulele bateriei și casetele electronice sunt asamblate, în altă parte, este pregătită carcasa din aluminiu a bateriei. Cea mai mare parte a lucrărilor de manipulare sunt efectuate de roboți, dar la unele stații au o rezervă manuală în cazul în care robotul nu este în măsură să facă treaba dintr-un anumit motiv. Carcasa masivă din aluminiu provine de la un furnizor extern. Aici pe linie este prevăzut cu toate componentele necesare, cum ar fi diverși conectori, garnituri, opriri și bucșe de șurub, dar și scutul de căldură extern care trece prin centrul carcasei. Acest scut protejează întreaga baterie de căldură de la sistemul de evacuare al mașinii care este plasat sub ea.
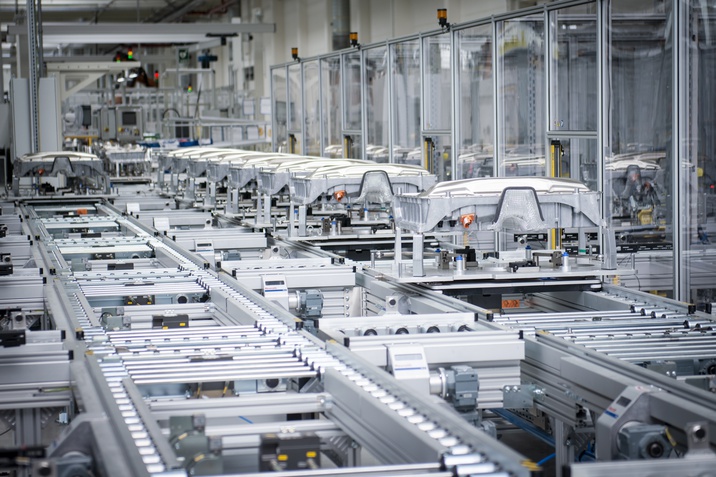
Când carcasa este complet asamblată, este rândul unui asistent poate neașteptat să-și intre în rol: un robot care folosește un aspirator pentru a se asigura că fiecare carcasă este lipsită de orice impurități care ar putea cauza probleme în timpul funcționării. După ce a fost aspirată, carcasa este pregătită pentru ceea ce este cunoscut sub numele de „căsătorie”. În timp ce în fabricarea automobilelor aceasta a însemnat în mod tradițional faza în care caroseria este unită împreună cu șasiul și motorul, aici înseamnă introducerea modulelor de baterii asamblate în carcasă, care este realizată de un robot. Un alt robot are grijă de procesul destul de complicat de înșurubare a băii și a modulului împreună. Sigiliul se află pe un suport. Complexitatea constă în faptul că șurubul și montura sunt conectate mai întâi.
Odată montată carcasa și modulele, sunt montate alte componente, în principal circuitul de răcire. Instalarea cablului de joasă tensiune este finalizată, iar carcasa este prevăzută cu material de umplere și suporturi de susținere. O soluție inteligentă este aplicată atunci când acestea sunt înșurubate împreună pe linie. "Șuruburile pentru fixarea suporturilor de susținere se află pe un cărucior special, prevăzut cu cântare, care poate spune dacă muncitorul a folosit numărul potrivit de șuruburi și nu a mai luat unul în plus care a căzut în carcasă, de exemplu", spune Otakar Mašek.
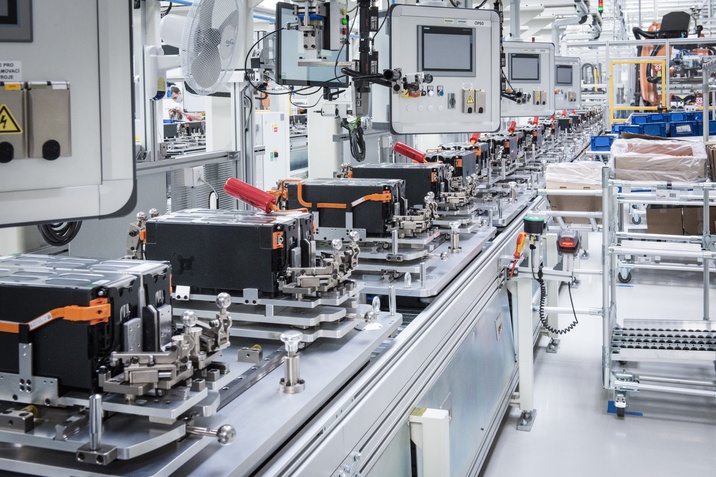
O altă metodă de control poate părea, de asemenea, neașteptată: după ce toți conectorii au fost atașați în interiorul bateriei, angajatul de la stația următoare folosește un marker pentru a face un punct pe locul conexiunii pentru a arăta că a efectuat o a doua verificarea vizuală a conexiunii. „Această cerință îl obligă pe angajat să privească efectiv conexiunea”, spune Mašek. Nu mai rămâne decât conectarea modulului la unitatea de control și bateria este gata să fie sigilată. Capacul carcasei este securizat cu o garnitură dublă: cauciuc și un lipici special. Capacul este înșurubat de un robot.
O MULȚIME DE TESTE
Montajul este urmat de o serie de teste. Primul este testul de etanșare, cu verificări separate ale etanșeității circuitului de răcire și a bateriei în ansamblu. Din când în când, o baterie cu aspect diferit apare printre bateriile testate. Aceasta este o unitate de probă care verifică dacă aparatul de testare a sigiliilor funcționează corect. Jeturi speciale pot simula defectele de etanșare, ceea ce adaugă o altă dimensiune verificării funcționalității aparatului de testare.

Când bateria a trecut testul de etanșare, poate trece la una dintre cele treisprezece etape de testare pentru o serie de teste electrice. Piesele de înaltă tensiune și joasă tensiune (comunicare) sunt verificate, iar testele sunt făcute pentru a se asigura că izolația funcționează corect. După ce bateria a trecut prin toate testele, aceasta este încărcată cu o capacitate de aproximativ 37%. Apoi i se oferă o etichetă de avertizare, propria sa etichetă în scopuri de identificare (această etichetă este de asemenea tipărită și atașată automat sub ochiul atent al unei camere) și alte câteva detalii. Apoi, bateria finită este expediată în depozit.
Linia de producție pentru baterii li-ion destinate hibrizilor plug-in ŠKODA
- Capacitate zilnică: 720 unități
- Capacitate anuală: 180.000 de unități
- Timpul ciclului: 88 secunde
- Durata de asamblare: aprox. 2 ore
- Număr de stații: 66
- Personal de linie: 58
- Suprafață de producție: 2.000 m2
- Investiție: 25,3 milioane EUR
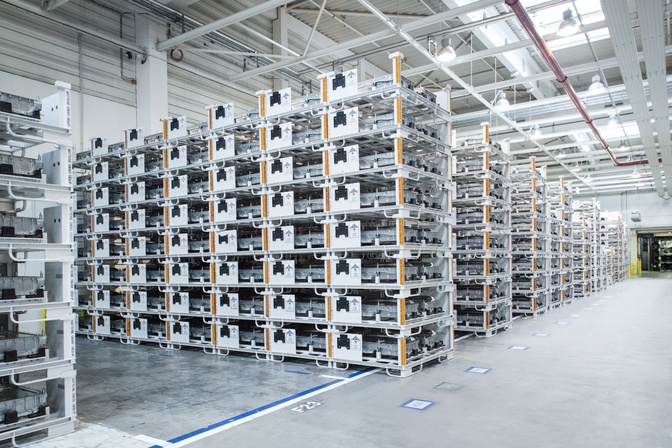